2021.09.13
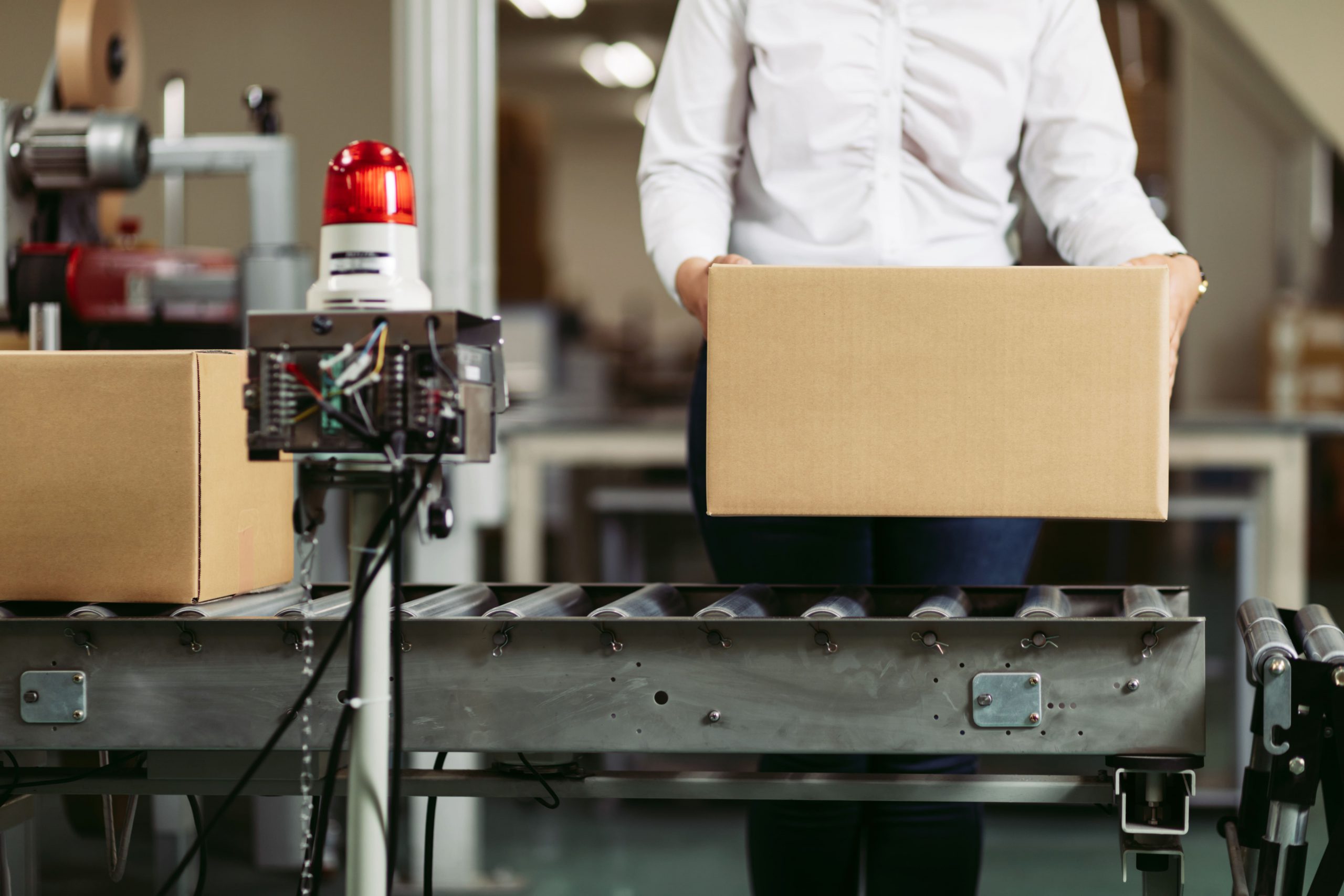
ECの運営において気を付けたいことが、出荷作業のミスです。なかでも誤出荷は、お客様からの信頼を落としてしまうことになるため、徹底的に防ぐ必要があります。
そこで本記事では、誤出荷の原因や影響、防ぐ方法を紹介していきます。
誤出荷を改善して物流業務の最適化を図りたい人は、ぜひ参考にしてみてください。
誤出荷を防ぐ重要性
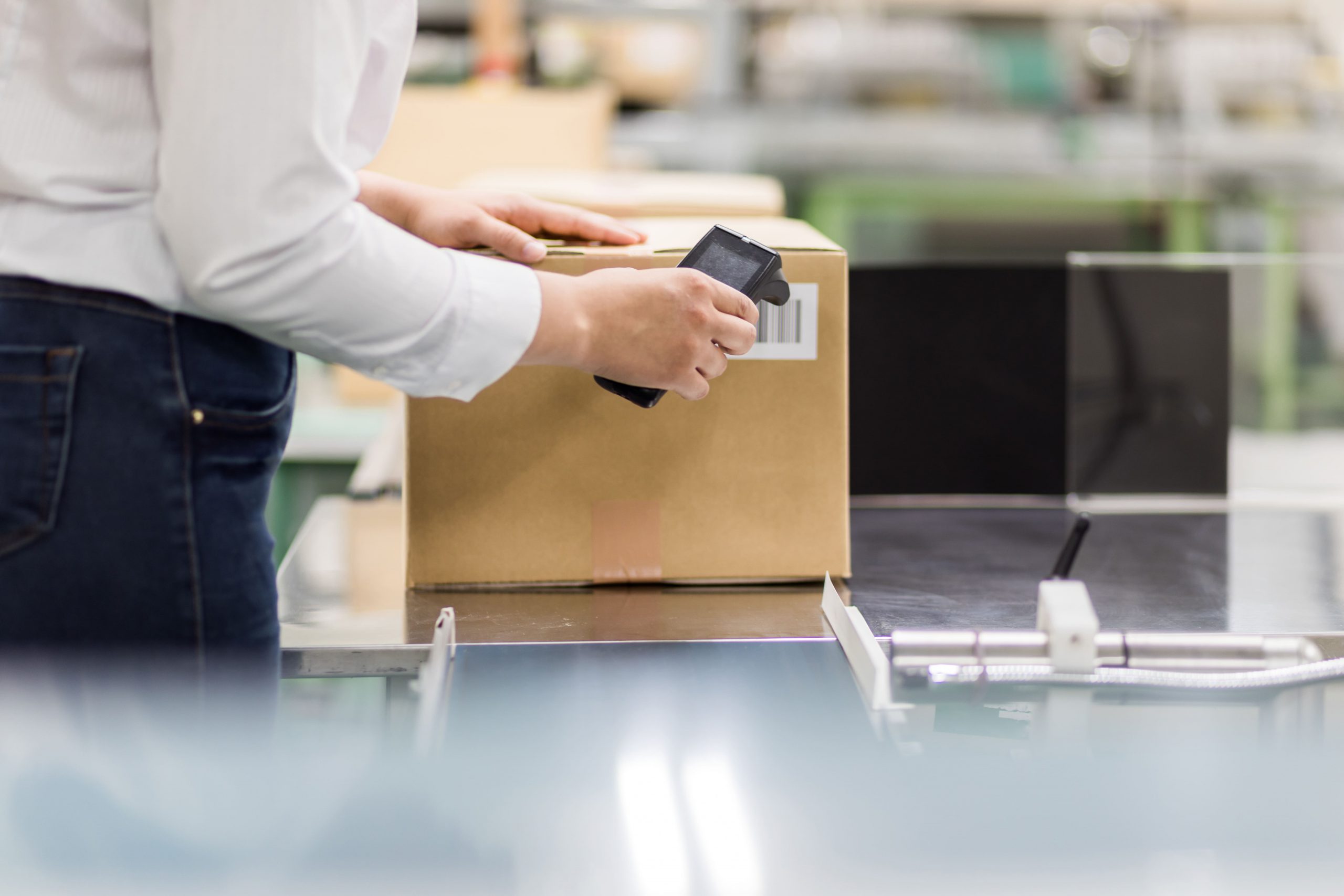
出荷作業において、手作業がある以上は誤出荷を完全にゼロにすることは難しいでしょう。しかし、ミスの発生数を抑えることは可能です。
誤出荷の改善を試みず何度も発生させてしまうと、自社サービスの信用問題に関わります。また、お客様からのクレーム対応や再出荷などによって業務量も増えてしまうでしょう。
そのため、誤出荷はできるだけ早く解決しなければならない問題なのです。
では、その誤出荷はどのようなことが原因で発生し、どのような影響を及ぼすのでしょうか。
誤出荷の問題
誤出荷が発生してしまう原因は様々ありますが、共通しているのは「手作業で出荷業務を行うときに起きる」という点です。
例えば、ピッキングの指示書を出すときにミスをすると、その後の作業を正しく行っても誤出荷が発生します。ピッキングをする商品を入れ間違えてそのまま出荷してしまうのも、ありがちなミスです。
そのほか、配送トラックの積み忘れなどの出荷漏れや、納品書・請求書の入れ間違いにも気を付けなければなりません。
作業ごとに厳重なチェックを行い、ミスの発生率を抑えることで誤出荷の減少につなげましょう。
誤出荷による影響
誤出荷で最も大きく影響を与えてしまうのが、「お客様からの信頼」です。
お客様のもとに届いた商品が別物だったり個数が少なかったりすると、もちろんお客様は不信感を覚えます。また、宛先を間違えて誤出荷してしまうと、お客様の個人情報が漏洩して、最悪の場合は悪質に利用される可能性も否定できません。
ほかにも、誤出荷が起きると在庫差異が発生してしまうでしょう。それにより、管理コストや廃棄リスクが増えるだけでなく、在庫差異の原因を解明するための無駄な労力が生まれてしまいます。
誤出荷による影響はお客様だけでなく自社にも及ぶため、誤出荷をなるべく抑えるように細心の注意を払うことが重要なのです。
誤出荷を防ぐポイント1.原因を追究する
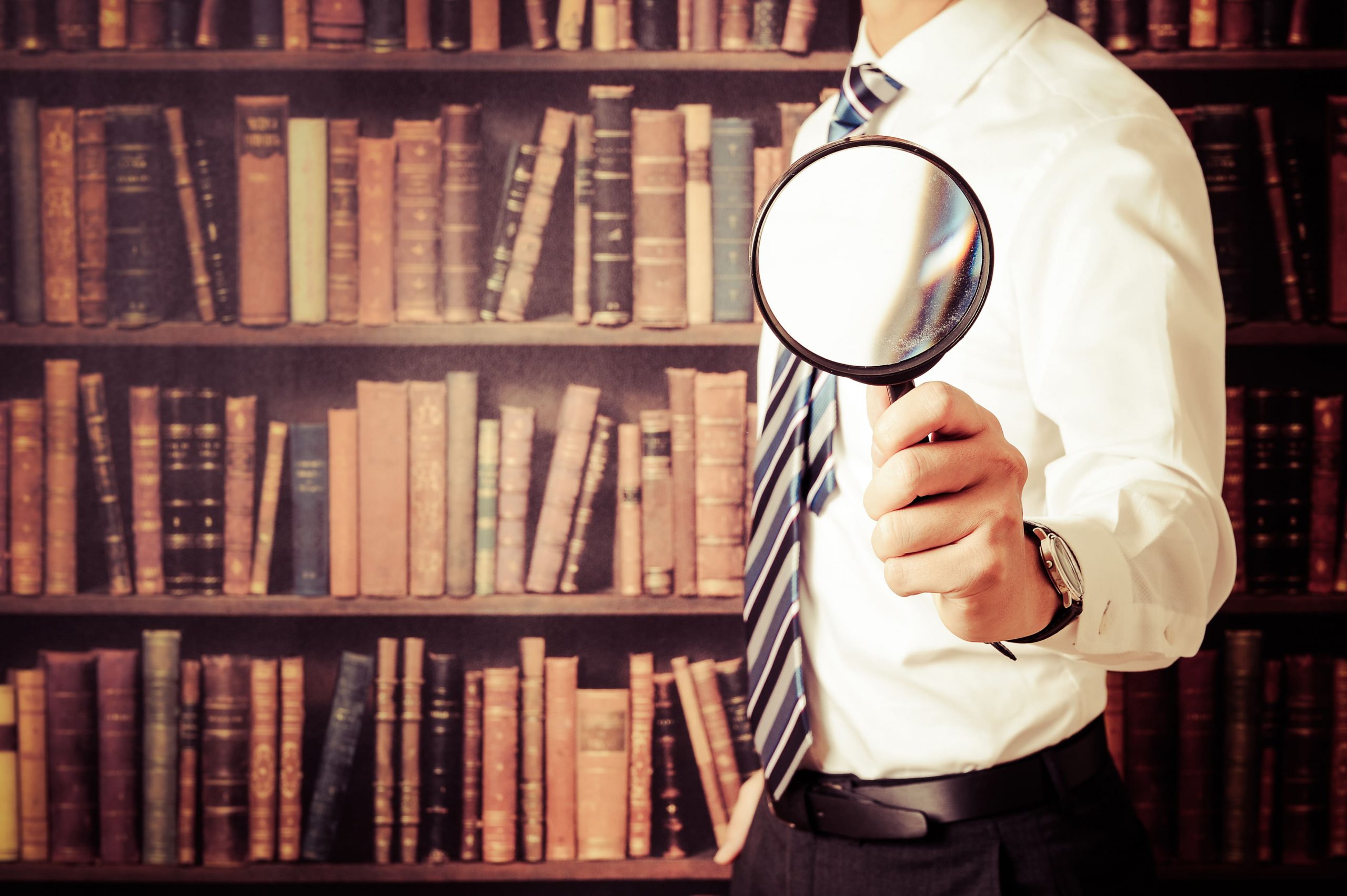
誤出荷を防ぐポイントとして大切なのが、「どのようなことが原因で発生したのかを追求すること」です。原因が分からないままだと誤出荷の防止策を的確に行えません。
例えば、ピッキングミスによる誤出荷ひとつをとっても、検品の精度の悪さや倉庫の不十分な整理状況など、あらゆる要因が考えられます。仮に倉庫の整理ができていないことが原因で誤出荷が発生したとしても、その原因が特定できていなければ「ピッキングミスしないように注意する」といった的外れな指示を出してしまう可能性があります。
そのため、誤出荷の原因を手作業によるミスと片付けず、どのようなことが原因で誤出荷が発生したのか追求する必要があるのです。
誤出荷は原因分析が難しい
誤出荷を防ぐためには原因を追求することが大切ではあるものの、あらゆる作業ミスが重なって起こっている可能性が高いため、誤出荷の原因を分析するのは難しいです。
誤出荷による影響が大きいことを考えると、一日でも早く改善したいでしょう。しかし、誤出荷が増えているときに焦ってすぐ解決方法に着手しても、作業効率が下がるだけでかえって誤出荷の発生率を高めてしまう恐れがあります。
まずは誤出荷が起こった原因を特定し、そこからひとつずつ紐解きながら解決策を考えることが大切です。
原因追及のコツ
誤出荷の原因を追求するには、まずどのような誤出荷が起きているかをひとつひとつチェックすることが大切です。
誤出荷の発生頻度や種類を記録しておくと、根本的な課題が見つかりやすくなります。また、発生件数によって「緊急度の高い課題はどれか」という優先順位を把握することができます。
まずは誤出荷の原因をすべて洗い出すことが、誤出荷を改善する重要なカギなのです。
誤出荷を防ぐポイント2.自社の業務を見直す
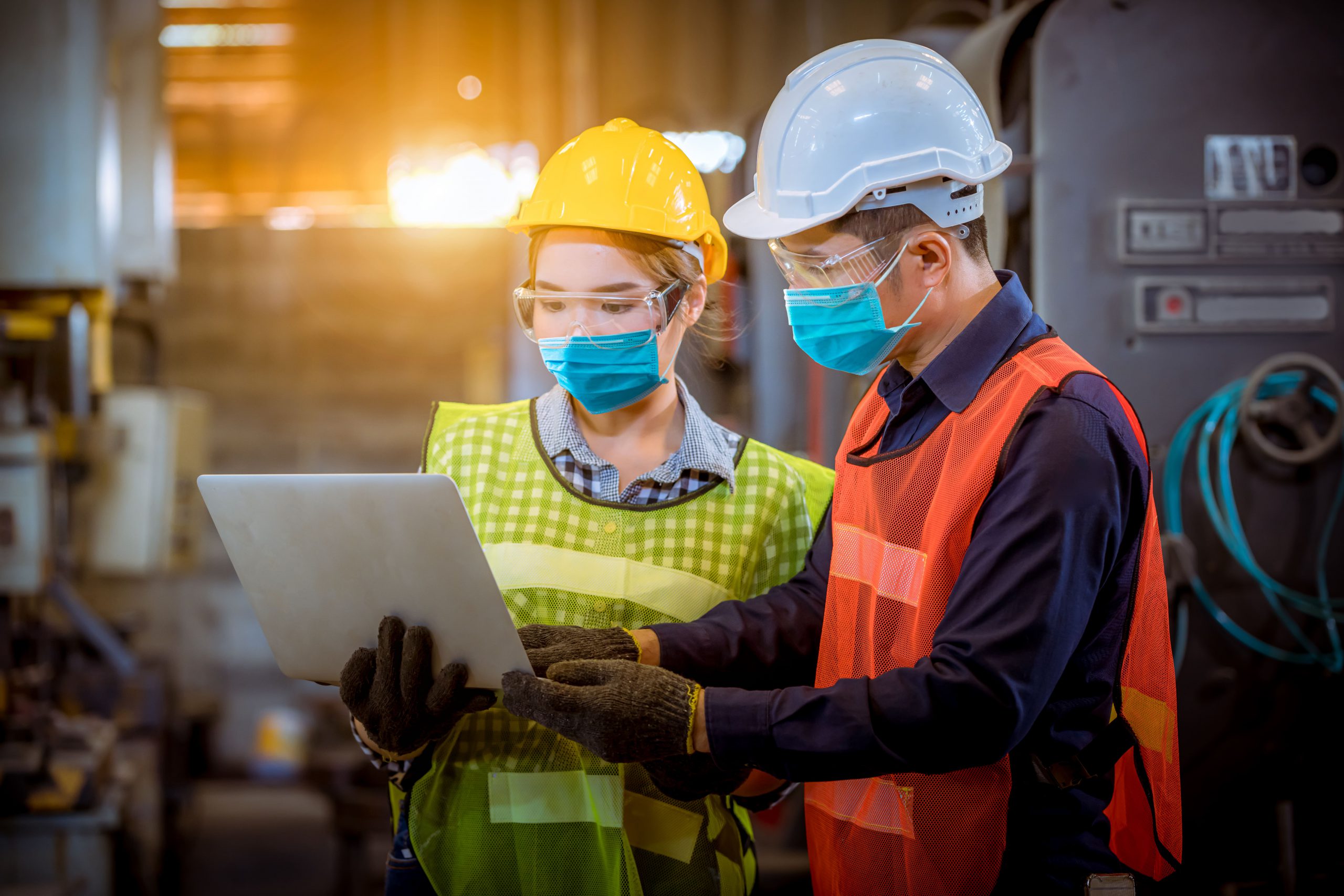
自社の業務ルールを見直すのも、誤出荷を防ぐポイントです。
では、具体的にどのように業務ルールを見直せば良いのでしょうか。
作業ルールを明確化する
自社の作業ルールが定められていないと、スタッフが独自の作業フローで業務を行ってしまい、思わぬところで人為ミスが起こる可能性があります。そのため、すべての作業員が同じ作業フローで業務を行うように作業ルールを明確にすることが大切です。
作業ルールを明確にしたあとは、独自のやり方で作業しないように業務フローを徹底させましょう。作業ルールが決められていたとしても、運用されていなければ意味がありません。
また、作業フローの明確化と同時に、作業の無駄がないか、チェック体制や人員配置は最適なのかを考えましょう。作業フローのなかに不要なものや非効率的なものが見つかれば、作業フローの改善につながります。
作業の環境を整える
作業スペースが狭いと、作業効率が下がるだけでなく、梱包する商品を間違えたり伝票を貼り間違えたりして誤出荷が起きる可能性があります。
十分な作業スペースが確保できれば、無駄な人為ミスを防いで誤出荷を改善しつつ、作業の効率化が狙えます。
作業スペースを十分に確保し、商品の積み方や仕分けが煩雑になっていないか注意しましょう。
誤出荷を防ぐポイント3.デジタル技術を活用する
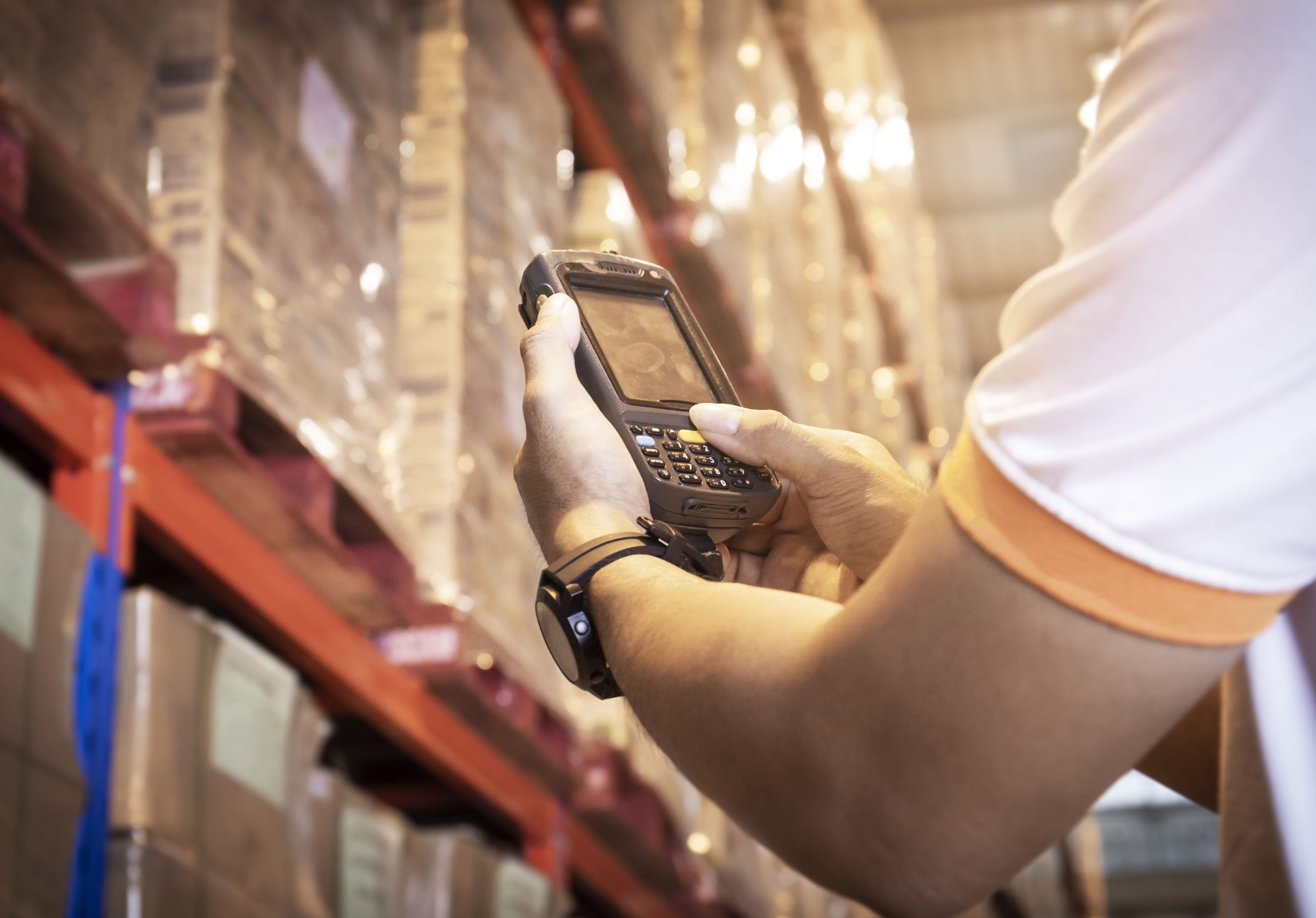
デジタル技術は、誤出荷を防ぐ有力な方法のひとつとして多くの企業に導入されています。
デジタル技術を活用することによって手作業で行っていた業務が自動化され、作業効率が向上するのはもちろん、ヒューマンエラーの回数が減って誤出荷の改善も期待できます。
バーコード・スキャナーは多くの企業でよく活用されています。商品をバーコードで管理できて、スキャナーでヒューマンエラーを改善できたり在庫を自動で記録したりできます。
誤出荷の防止だけでなく、棚卸や出荷検品作業といった物流業務の効率化も狙えるでしょう。
誤出荷を防ぐポイント4.システムを導入する
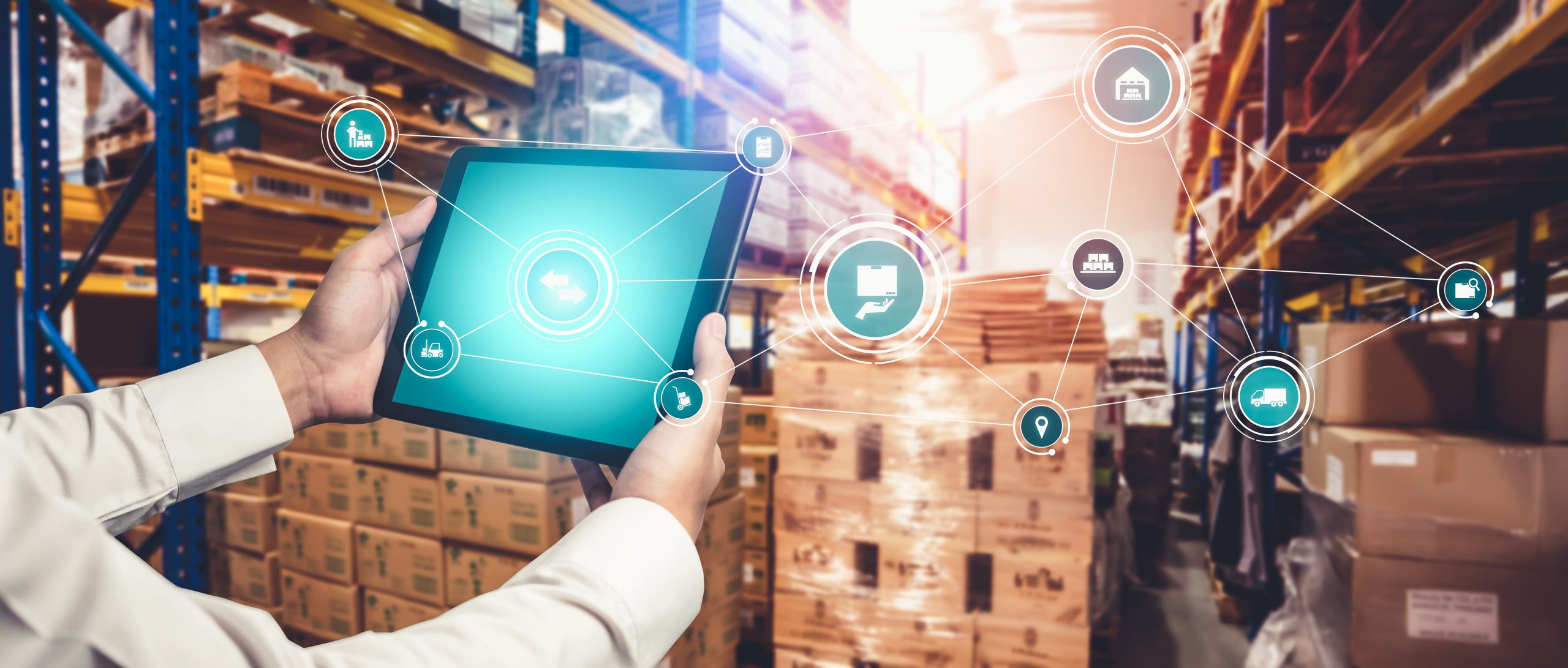
デジタル技術と同様に、システムを導入するのも誤出荷を防ぐうえで効果的です。こちらも、ヒューマンエラーが改善されて誤出荷の防止につながります。
多くの企業が導入しているのが、WMS(倉庫管理システム)。入出庫における最適なロケーションを指示しつつ、在庫管理を自動化します。
システム導入をお考えの方は、はぴロジの自動出荷管理システム「HAPILOGI ASIMS」をご検討ください。あらゆる出荷業務やショップデータの自動化だけでなく、複数の倉庫から適切な倉庫を選んで自動で出荷することが可能です。
さらに、さまざまなWMS(倉庫管理システム)やERP、ECカート、ECモールと連携しているため、一括管理もできます。
システムを導入すれば誤出荷の防止はもちろん、作業時間を短縮化も図れるのでおすすめです。
誤出荷を防ぐポイント5.倉庫移管をする
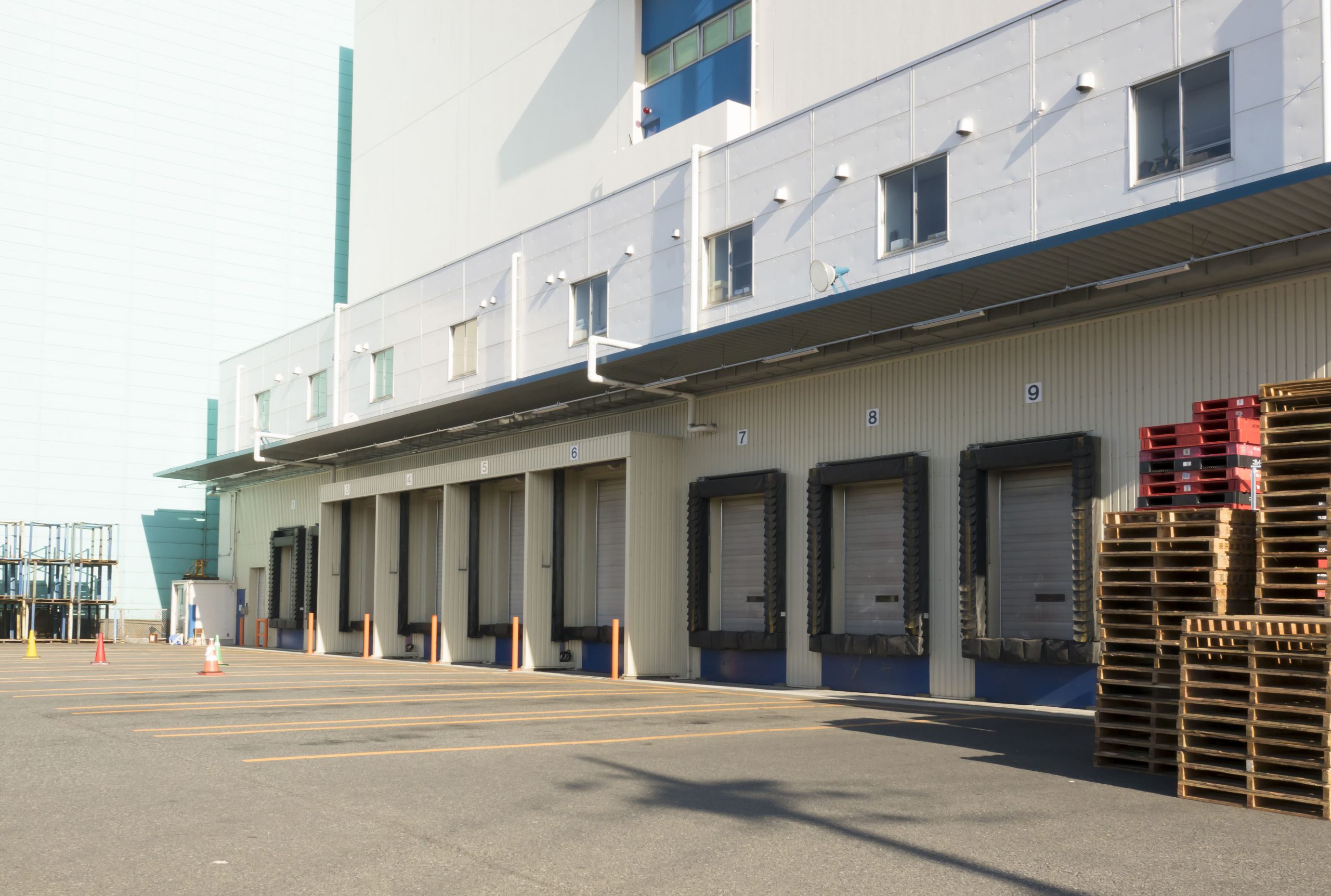
倉庫業務をアウトソーシングした後、誤出荷が連続して委託先で起こる場合には、アウトソーシング拠点の変更も検討する必要があります。
倉庫移管は事業規模が大きいほど労力やコストがかかり、作業も複雑化します。そのため、逆算して余裕のあるスケジュール作りと役割分担を明確にしておくことが重要です。
特に時間がかかるのが移転先倉庫とのデータ連携で、場合によってはシステムを改修する必要があり、さらに時間がかかってしまうでしょう。
はぴロジであれば倉庫移管に関するご相談も可能です。EC事業者様ごとに担当のCSがつき、全国の拠点からサービスや業界、発送方法などを考慮した最適な倉庫をご提案いたします。
さらに、倉庫移管の際に発生し得るシステム開発やシステム変更をすることなく、データ連携を行うことが可能です。
まとめ
今回は、誤出荷の原因や影響、防ぐ方法について紹介しました。
誤出荷はお客様からの信頼を損ない、機会損失となる可能性があるため、できるだけ早めに解決すべき問題です。
手作業の出荷業務ミスが重なって発生しているケースも多いことから、ゼロにすることは難しいものの、誤出荷の発生数を極力減らす努力はできます。
本記事の内容を参考にして、自社で発生している誤出荷の改善、防止に努めましょう。
はぴロジASIMSは、次期バージョンのクラウドシステムはぴロジlogiec<ロジーク>として、刷新いたしました。 「logiec」は、あらゆるECカートやECモール、受注管理システムとWMS(倉庫管理システム)などのあらゆるシステムをつなぎ、データ連携をシームレスに実現します。 |
---|